Biofuels from Lignocellulosic Biomass
Gasifier Technologies
Various gasification technologies are available, classified by the contact and flow of gas through the reactor:
- Fixed-bed gasifiers
- Fluidized-bed gasifiers
- Entrained-flow gasifiers
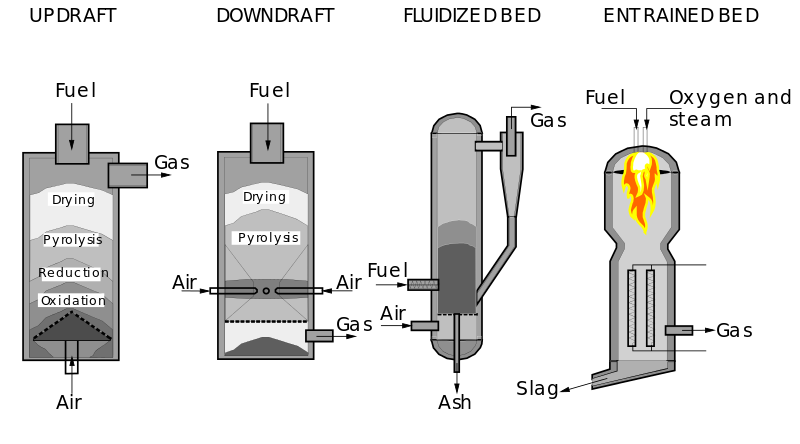
Gasifier Types_EN by Kopiersperre, translated by HOOU (CC BY-SA 4.0)
Fixed bed gasifiers
In fixed bed gasifiers the biomass enters the reactor at the top. The fuel slowly moves downward due to gravity and decomposition processes to the bottom of the reactor where it is exposed to the gasification agent, which is directed into the reactor from the bottom in a countercurrent flow (updraft reactors, see far left figure above). If the air is fed into the reactor in an upper part, the gasification agent moves into the same direction like the fuel. These reactors are therefore called downdraft reactors (see second picture from left in the figure above). Thereby different zones are developing where the different stages of gasification process occur.
The hottest zone of the updraft reactor is at the
bottom because there the gasification agent (air) is fed in. This is where the
heat needed for the process is generated and the product gas is produced. Due
to high temperatures ash components that do not thermally decompose liquefy and
form slag which has to be removed below. The upstreaming hot gas is used for
warming up and drying the fuel in the zones above. In the reduction zone above
the oxidation zone the carbon dioxid (CO2)
produced during oxidation is partly reduced to carbon monoxide (CO) and
occuring water vapour to hydrogen. Above the reduction zone is the pyrolytic
zone, where the fuel is thermo-chemically cracked with the heat from the
oxidation zone. The product gas is released at the top of the reactor. On its
way through the reactor the gas is cooling down.
Updraft reactors have several advantages:
- high gasification efficiency
- low temperatures of the product gas (100-200°C)
- very low alkali metal contents
- low particle content in the product ga
- low requirements for fuel preparation
The disadvantages are:
- considerable amounts of undesired components, like tars in the product gas
- quite high water vapor content in the product gas
- for further use, the product gas quality requirements cannot be met so easily
Downdraft gasifier
In downdraft gasifiers the fuel and the
gasification agent are moving in the same direction - from the top to the
bottom. The fuel is dried and pyrolized in the upper part in the absence of
air. Then it moves down in the very hot oxidation zone (>1000°C). Long-chain
organic compounds are cracked into short-chain and low-tar gaseous compounds.
This compounds and the resulting coke and ash move further in the reduction
zone where they are reduced.
Advantages:
- product gas has low tar contents and can be used without further gas cleaning (e.g. for liquid fuel production)
Disadvantages:
- high product gas temperatures (600-800°C)
- high requirements for fuel size and water content (<20%)
- problems occure in big reactors (temperature in some parts too low) and in partial load operation.
Commercial use of this technology has not been achieved to date. The operation is partly unsatisfactory for technical and economic reasons.