5. Manufacturing of viscose
Learn how viscose i commonly manufactured.
5.1 Production processes
The raw material
The wood component cellulose is used as the starting material for viscose production. Depending on the tree species, wood consists of 30 to 70 % cellulose. It provides stability in the plant cell walls. A cellulose molecule consists of hundreds to thousands of glucose units (Figure 1), which are linked via ß-1,4-glycosidic bonds (Figure 2).
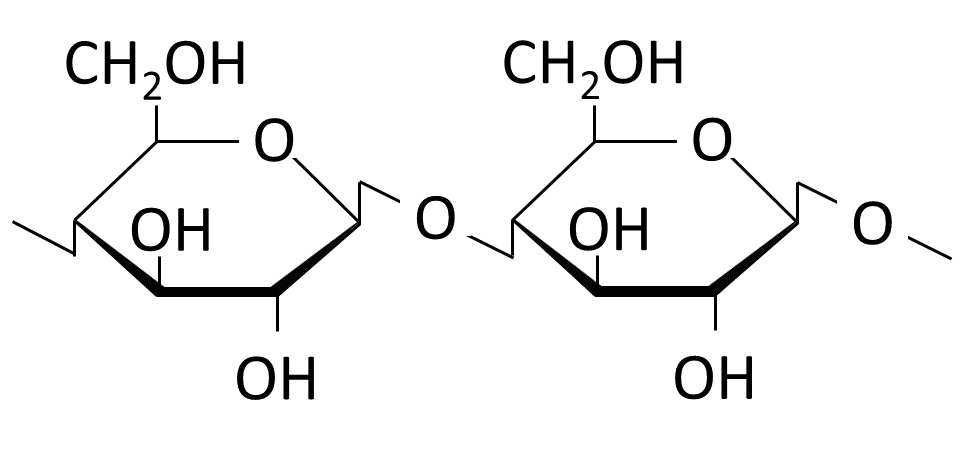
From wood to cellulose
Acids are usually used to separate the cellulose from the lignin. There are two main processes that are also used in pulp production:
- the sulphate process
- the sulphite process
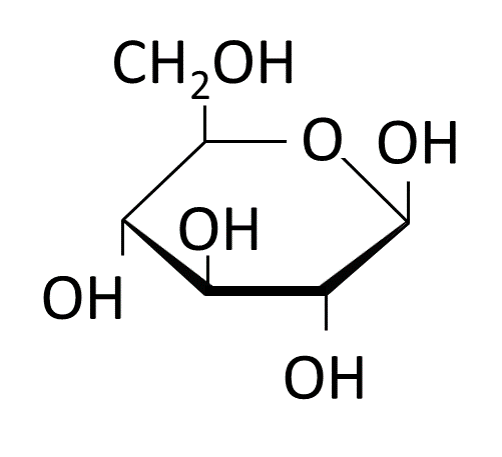
In order to better break down the wood, it must first be debarked and shredded. It is then boiled at 130-150 °C with the addition of sodium hydroxide and sodium sulphide (sulphate process) or calcium hydrogen sulphite, magnesium bisulphite and sulphurous acid (sulphite process). The cellulose obtained is bleached by oxidation and dried. The remaining lignin and the chemicals used are incinerated together. On the one hand, energy can be obtained from this, and on the other hand, the chemicals react due to the high temperatures and collect at the bottom of the boiler, from where they can be recovered more easily.
Production of a spinning solution from cellulose
In a further step, the fiber structure of the pulp is dissolved using 18-22% caustic soda. Alkali cellulose is formed, which is then defibered to increase its surface area. Depolymerization of the alkali cellulose takes place during a 'maturing period' at a constant temperature and humidity. Carbon disulphide is then added and treated for three hours at 25-30 °C, whereby some of the hydroxyl groups in the alkali cellulose combine with the carbon disulphide. The result is cellulose xanthate - an orange-yellow, viscous mass reminiscent of honey. This is also the origin of the name of the fiber later produced from it: viscose.
To produce the spinning solution, the cellulose xanthate is dissolved in an aqueous sodium hydroxide solution (approx. 5 % NaOH by weight) and must then polymerize for a further 2-3 days under vacuum.
Generation of the fiber
The actual fiber is formed when the solution described above is pressed through nozzles into an acidic precipitation bath. The size of the nozzles determines the thickness of the thread and varies between 25 and 250 µm. The precipitation bath contains sulphuric acid, sodium sulphate and small amounts of zinc sulphate. The chemical reactions in the precipitation bath cause the dissolved cellulose to regenerate and coagulate into the desired fiber, which is removed from the precipitation bath and stretched while still soft, thereby permanently stretching it. This makes the fibers more resistant to abrasion and tension.
Post-treatment of the fibers
After stretching, the fibers are cleaned of any chemical residues using hot washing, alkali salts or bleaching agents. If this is not done, the fibers could subsequently be destroyed again. Soap-like substances are then applied to make the fibers more supple.
Viscose fibers have a high moisture absorption capacity, but are also quick-drying. They do not become electrostatically charged and can be easily dyed. Viscose fabrics are mechanically, chemically and thermally stable, yet soft, flowing and have a silky sheen. This is why viscose is sometimes referred to as artificial silk.
Handling of the chemicals used
The many chemicals in the precipitation bath, some of which are toxic, are regenerated to conserve resources and protect the environment. Hydrogen sulphide is separated by gas scrubbing. Sodium sulphate is removed and used in the detergent industry. The carbon disulphide is either incinerated or recovered using an activated carbon filter.
The following video summarizes the entire production process.