4.3 Applications in the Industry Sector
Website: | Hamburg Open Online University |
Kurs: | Green Hydrogen |
Buch: | 4.3 Applications in the Industry Sector |
Gedruckt von: | Gast |
Datum: | Donnerstag, 14. August 2025, 04:36 |
Beschreibung
Nowadays in the industrial sector, fossil raw materials are not only used as energy sources, but also as basic materials in many processes. Examples of this are the production of plastics, which is largely based on crude oil, or the production of fertilisers, which requires natural gas. In this chapter you will learn that green hydrogen plays a crucial role in the transformation of the industrial sector towards climate neutrality.
Steel Making
The most important raw material for steel production is naturally occurring iron ore. Iron ores used for steel production today are mostly iron oxides - in other words, chemical compounds of iron with oxygen (e.g. iron(III) oxide, Fe2O3). In order to to produce steel, the iron must be separated from the oxygen. In the classic blast furnace process, the oxygen is separated with the help of coke, a fuel made from coal. The following reaction equation is a simplified representation of the chemical process taking place:
Fe2O3 + 3 CO --> 2 Fe + 3 CO2
The carbon contained in the coke acts as a so-called reducing agent and reacts with the oxygen from the iron oxide at first to form carbon monoxide and later carbon dioxide. In addition, the coke provides the energy needed to reach the temperatures of up to 1600 °C in the blast furnace required to reduce the iron ore. So-called pig iron is produced in the blast furnace. This pig iron contains many by-products such as sulfur, phosphorus and carbon and generally cannot be used directly. The pig iron is processed into crude steel in the oxygen converter, where the undesirable by-products are removed with the help of oxygen.
Steel production using the blast furnace route is a very CO2-intensive process. Steel production alone, currently, accounts for approximately 6 % of Germany's total greenhouse gas emissions.
Steel production using the blast furnace route is a very CO2-intensive process. Steel production alone, currently, accounts for approximately 6 % of Germany's total greenhouse gas emissions.
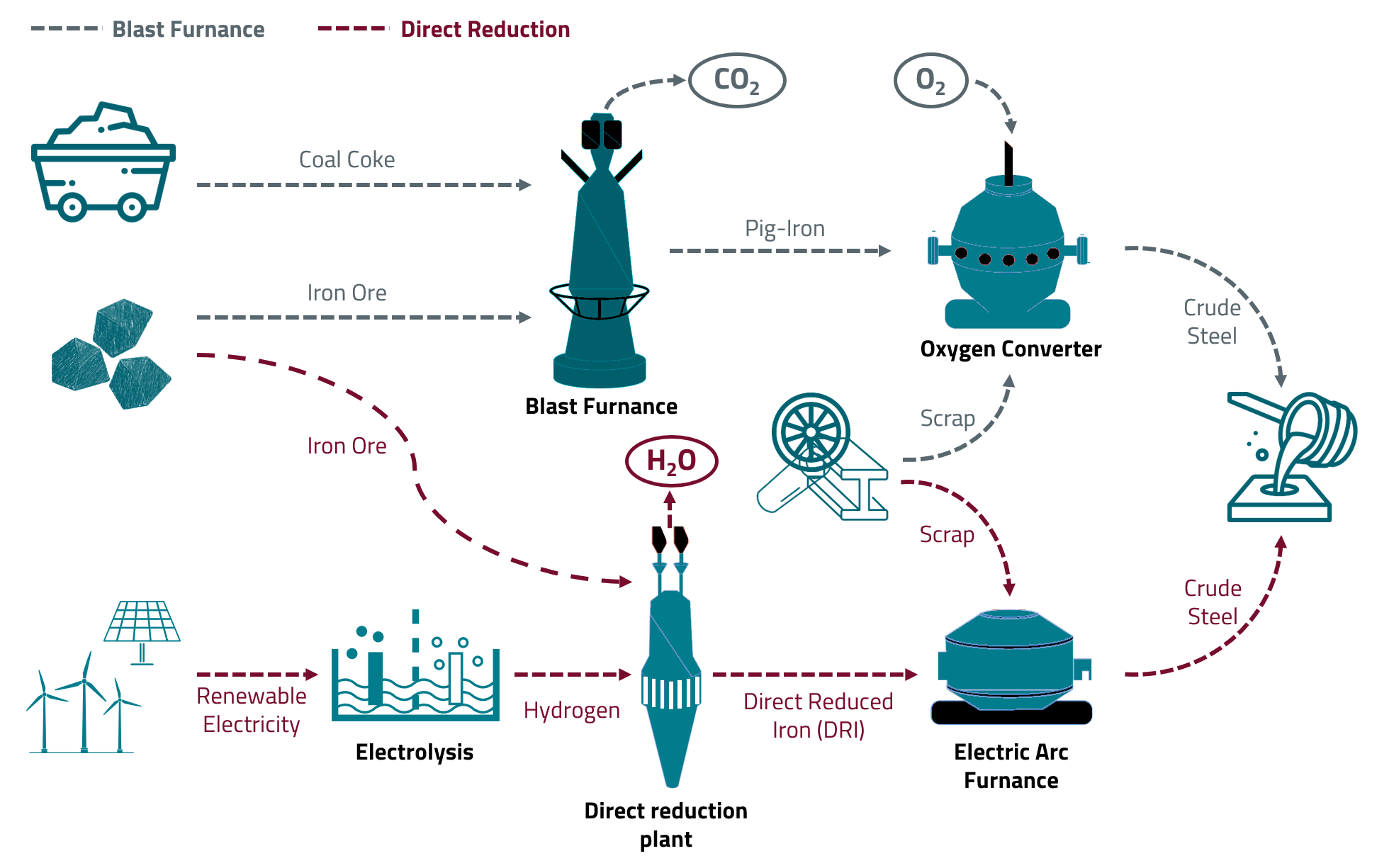
Fe2O3 + 3 H2 --> 2 Fe + 3 H2O
The product of the direct reduction process is a material called sponge iron. Similar to the pig iron from the blast furnace the sponge iron usually contains various impurities such as sulfur or phosphorus. The separation of impurities and further processing into crude steel is carried out in electric arc furnances. In this process, the sponge iron is heated to up to 3000 °C using electrical energy. Electric arc furnaces are already used on an industrial scale today and are mainly applied for the processing of steel scrap and the production of quality and stainless steels. The direct reduction of iron ore with the help of hydrogen, though, has not yet been realised on an industrial scale. Various steel manufacturers have announced pilot projects and expect to be able to produce climate-neutral steel using hydrogen by 2030 at the latest.
The combination of hydrogen-based direct reduction and electric arc furnance makes it possible to produce steel exclusively on the basis of renewable energies. However, the electricity demand of this production route (for the production of the green hydrogen and the operation of the electric arc furnace) is enormously high. If Germany's entire steel production (approx. 40 million t/a) were to be converted to the hydrogen route, around 190 TWh of electrical energy would be required annually. This corresponds to more than one third of Germany's total current electricity consumption.
Refinery
Before crude oil can be used as fuel, it must be treated. In the course of refining, the crude oil is further processed into different fuel products, such as diesel, petrol, kerosene or heating oil. Already today, hydrogen is used in various steps of this crude oil refining. The most important processes are hydrocracking and desulphurisation. The hydrocracking process describes the conversion of long-chain hydrocarbons (heavy oils) into short-chain hydrocarbons (light oils). For this purpose, the crude oil is treated with a hydrogen-containing gas. In desulphurisation, hydrogen is added to a fuel. Heating the mixture causes a reaction between the hydrogen and the sulphur contained in the feedstock. The resulting hydrogen sulphide can then be removed.
Since hydrogen is a by-product of other refinery processes in considerable quantities, refineries only produce part of the hydrogen required for hydrocracking and desulphurisation in a targeted manner. In the recent past, global hydrogen consumption by oil refineries has steadily increased. The reasons for this were, on the one hand, the still increasing consumption of fossil fuels and, on the other hand, stricter requirements on the sulphur content of fuels.
Due to the ongoing electrification of road traffic - which means that electric vehicles are replacing classic cars with combustion engines - the demand for fossil fuels is expected to decline in the future. However, this does not automatically imply that refineries as major consumers of hydrogen will disappear in the future. In the future, refineries may produce the e-fuels mentioned in the first section of this chapter, which require large quantities of green hydrogen. Thus, as a first step, refineries could substitute the grey hydrogen they currently use with green hydrogen and thereby reduce their CO2 emissions. In a second step, they could then gradually shift their production processes to green hydrogen-based e-fuels.
Due to the ongoing electrification of road traffic - which means that electric vehicles are replacing classic cars with combustion engines - the demand for fossil fuels is expected to decline in the future. However, this does not automatically imply that refineries as major consumers of hydrogen will disappear in the future. In the future, refineries may produce the e-fuels mentioned in the first section of this chapter, which require large quantities of green hydrogen. Thus, as a first step, refineries could substitute the grey hydrogen they currently use with green hydrogen and thereby reduce their CO2 emissions. In a second step, they could then gradually shift their production processes to green hydrogen-based e-fuels.
Chemical Industry
As already mentioned in Sections 3.2 and 4.1, large quantities of hydrogen are used today to produce ammonia and methanol. While ammonia is a central feedstock for the production of fertilisers, methanol is further processed into a variety of downstream products. For example, methanol is used as a raw material for the production of many types of glue or resins. Resins, for their part, can be further processed into paints and varnishes, among other things.
As shown in Section 4.1, methanol and ammonia are nowadays produced almost exclusively from grey hydrogen based on natural gas. A first step on the way to a climate-neutral chemical industry would therefore be to replace this grey hydrogen with green hydrogen. As the chemical industry moves away from fossil raw materials, however, the demand for methanol in the future could far exceed the current demand. Thus, numerous basic materials of the chemical industry are currently still produced on the basis of crude oil or natural gas. Important examples of such basic materials are ethylene and propylene. These two chemicals are, for example, starting materials for the production of a large number of plastics. The so-called "Methanol-to-Olefins" process makes it possible to produce ethylene and propylene from methanol. If the methanol is in turn produced from green hydrogen, crude oil and natural gas can be completely eliminated.
If the chemical industry is to run completely without fossil fuels in the future, green hydrogen would therefore be a central component of new, climate-neutral production processes.
As shown in Section 4.1, methanol and ammonia are nowadays produced almost exclusively from grey hydrogen based on natural gas. A first step on the way to a climate-neutral chemical industry would therefore be to replace this grey hydrogen with green hydrogen. As the chemical industry moves away from fossil raw materials, however, the demand for methanol in the future could far exceed the current demand. Thus, numerous basic materials of the chemical industry are currently still produced on the basis of crude oil or natural gas. Important examples of such basic materials are ethylene and propylene. These two chemicals are, for example, starting materials for the production of a large number of plastics. The so-called "Methanol-to-Olefins" process makes it possible to produce ethylene and propylene from methanol. If the methanol is in turn produced from green hydrogen, crude oil and natural gas can be completely eliminated.
If the chemical industry is to run completely without fossil fuels in the future, green hydrogen would therefore be a central component of new, climate-neutral production processes.