9. Bio-based aviation fuel
Website: | Hamburg Open Online University |
Kurs: | Process engineering for the bioeconomy |
Buch: | 9. Bio-based aviation fuel |
Gedruckt von: | Gast |
Datum: | Sonntag, 7. September 2025, 07:18 |
Beschreibung
This book is about advanced fuels based on agricultural biomass resources and their production.
9. Bio-based aviation fuel
There are many different methods of biofuel production. Some are already mature and in use, others are still at an experimental stage or in the trial phase. In the future, synthetic fuels based on abiotic renewable energy sources (e.g. renewable electricity) will become increasingly important.
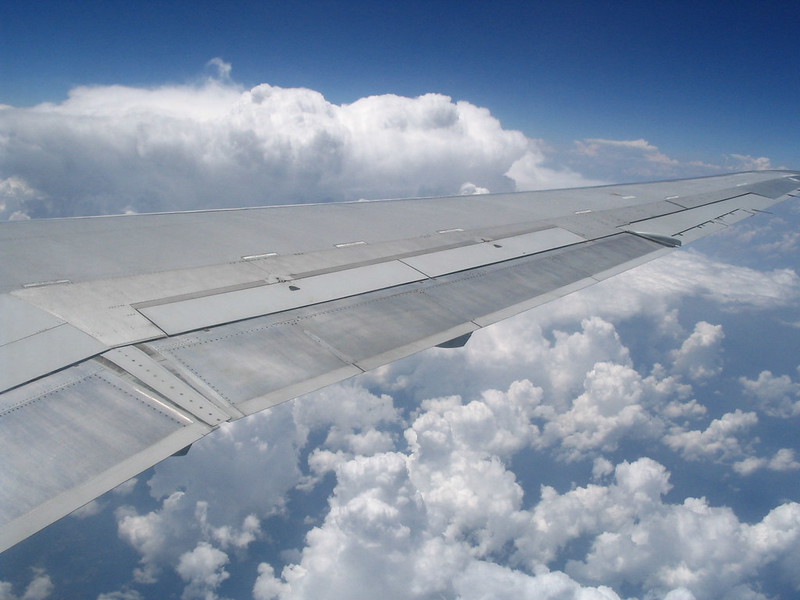
What you should know
- A number of processes for the production of Sustainable Aviation Fuels (SAF) have already been approved by the International Civil Aviation Organization (ICAO), including HEFA, Alcohol-to-Jet and Fischer-Tropsch synthesis
- SAFs are not used in their pure form, but are blended with up to 50% fossil kerosene
- The production of kerosene using genetically modified yeasts (SIP) is also being tested
9.1 Which bio-based fuels are already available?
Bioethanol and biodiesel are among the most widely used biofuels and are mostly used in road vehicles or blended with conventional fossil-based fuel. Bioethanol is produced via a fermentation process with subsequent distillation. Currently, the main raw materials used are corn (in the USA) or sugar cane (in Brazil). Depending on the production process and raw material basis, a distinction is made between FAME (fatty acid methyl ester) and HVO (hydrognenated vegetable oil) or, synonymously, HEFA (hydroprocessed esters and fatty acids) in the case of biodiesel. FAME has a different chemical composition to fossil diesel and is therefore not suitable in its pure form for conventional diesel engines and is therefore only blended in. HVO and HEFA, on the other hand, are fully compatible. If you want to learn more about the different production processes and raw materials, you can take a look at chapter 2 of the educational material on the topic of future-oriented fuels on the HOOU platform.
Classification of biofuels
Biofuels can be divided into 3 types, which are also referred to as generations. The characterization depends on the raw materials used and the level of their technological maturity:
1st generation fuels
- Conventional biofuels
- are based on sugar, starch or vegetable oil, i.e. biomass that is also used as food
- the production process is well mastered and is already widely used and commercialized
2nd generation fuels
- are based on cellulosic biomass (e.g. wood, straw or maize straw)
- do not compete directly with food production, but still require land resources
- the processing technology is sometimes immature and costly, as cellulose-containing material must be pre-treated before conversion
3rd generation fuels
- use special microorganisms such as algae as raw materials
- Algae are a large group of photosynthesizing organisms with around 30,000 known species
- Biofuel production from algae is well established on a small scale, but not yet economically feasible on an industrial scale
There is now also talk of a 4th generation of fuels. This refers to biofuels that are produced from genetically modified algae or plants. Genetic modification can eliminate the disadvantages of “normal” plants, such as a low fat content or low growth rates.
In some cases, hydrogen from renewable sources, biomethane, synthetic biofuels and fuels from renewable electricity, sometimes in combination with carbon capture and storage, are also referred to as fourth-generation fuels.
Status quo production
Im Jahr 2021 wurden 159 Milliarden Liter Biokraftstoffe produziert (IEA, 2022). Große Mengen der derzeit verwendeten Biokraftstoffe werden aus Pflanzenölen gewonnen. Bioethanol ist der weltweit am häufigsten verwendete Biokraftstoff. Im Jahr 2021 wurden weltweit ca. 103 Mrd. Liter produziert. USA, Brasilien und die Europäische Union sind die größten Erzeugerländer (Renewable Fuels Association, 2022: ).
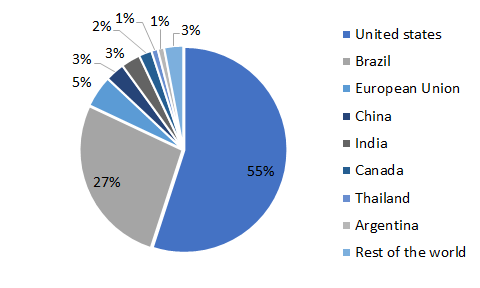
Global production of biodiesel and biokerosene is significantly lower.Around 54 billion liters were produced in 2021. The production of biodiesel through transesterification (FAME) accounted for around 80% of this volume, while hydrogenated biodiesel (HVO and HEFA) only accounted for 17%.
HEFA technology is currently used in most cases for the production of SAF (Shahriar & Khanal, 2022: ).Waste fats, oils and animal fats are used as raw materials. Biodiesel production using the alcohol-to-jet process from municipal waste or forestry and agricultural residues is much lower (Shahriar & Khanal 2022).
In 2021, however, only 0.1% of global kerosene demand was covered by SAF. According to the IEA (2022), the share is expected to increase to 5% by 2030.
Aviation fuels
Aviation fuels must meet very specific requirements in terms of combustion quality and safety.
The fuel must:
- not ignite uncontrollably
- not form deposits
- not become electrically charged
- not freeze at temperatures below -30 °C
Of course, these requirements also apply to bio-based aviation fuels.
The term SAF - Sustainable Aviation Fuel - has been used for some time by the aviation industry for alternative fuels based on biogenic raw materials and also includes electricity-based fuels. At present, however, these SAFs are not used in their pure form, but are blended with up to 50% fossil kerosene.
9.2 How are SAFs manufactured?
The basic principles of the most important, already approved production processes for the manufacture of bio-based SAF are explained below. A complete and up-to-date overview of the production processes approved to date by the American Society for Testing and Materials (ASTM) can be found at the ICAO.
HEFA process
All vegetable oils or animal fats can be used to produce the fuel. However, a process based on algae has also already been approved. On a large scale, used cooking oils (e.g. frying fat) and animal fats from slaughterhouse waste are already being used to produce biodiesel or biokerosene, particularly by the Finnish company Neste.
Process steps
Process step | Procedure |
1 | Cleaning the oil or grease, removing impurities |
2 | Esters and double bonds that make up oils and fats must be removed. Hydrogen is used for this - which is why the process step is called hydrogenolysis. Oxygen is also removed from the product as a by-product, as it reacts with the hydrogen to form water. The process requires catalysts made of cobalt or nickel, temperatures of 280-340°C and pressures between 50 and 100 bar. |
3 | Combined process of cracking and isomerization, in which the resulting long-chain n-alkanes are converted into shorter, branched molecules and open bonds are saturated with hydrogen. Precious metal catalysts and hydrogen are used for isomerization. The result is a higher quality crude oil that does not become viscous as quickly at low temperatures. |
4 | Separation of the product stream into the various alkanes with similar properties. During subsequent distillation and rectification, the remaining liquid products are separated into three fractions - naphtha, kerosene and diesel - based on their different boiling points. Various additives are added to meet the requirements for aviation fuel. |
Flow chart HEFA process
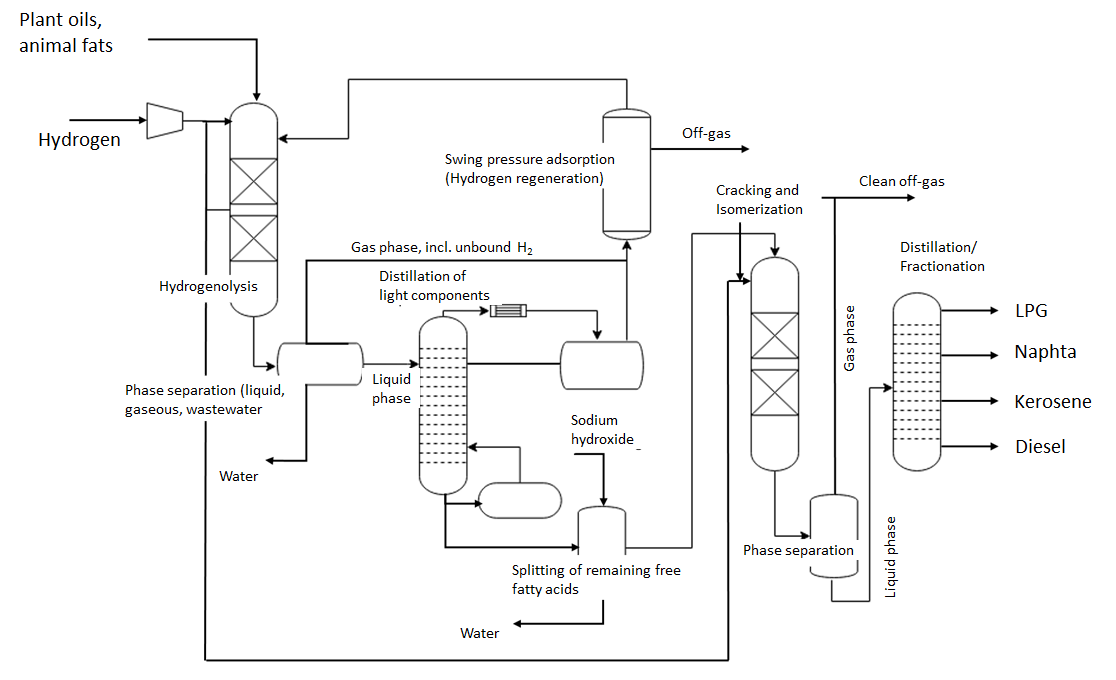
Fischer-Tropsch synthesis from biogas
In order to be able to produce a fuel from municipal waste or forestry and agricultural residues, the solids must first be converted into a gas. This process takes place in biogas plants and was explained in detail in chapter 8 of this learning offer.
The further steps involved in liquefying the gas are briefly explained in the following table.
Process step | Procedure |
1 | Methane reforming is used to produce a synthesis gas containing carbon monoxide (CO) and hydrogen (H2) from the biomethane. Hydrogen to carbon monoxide ratios of 2.1 are most suitable for the next process steps. |
2 | In order to achieve the optimum ratios, the syngas must be conditioned. This mainly involves removing CO and adjusting the hydrogen content. Impurities are also removed. The hydrogen content should be at least 50%. The optimum ratio of H2 to CO depends on the atalyzers used in the subsequent Fischer-Tropsch synthesis. |
3 | Fischer-Tropsch synthesis is used to produce paraffins, olefins and oxygenated compounds from syngas. Mainly straight-chain n-alkanes, less branched iso-alkanes are produced, which, unlike products made from crude oil, do not contain any sulphur or aromatics. The presence of iron, cobalt or nickel catalysts is required for the reaction. The temperatures and pressures required also depend on the catalyst material used. |
4 | Separation by distillation and rectification of the product stream into the fractions kerosene, naphtha, liquid gas and diesel on the basis of the different boiling points. Long-chain waxes are also produced, which have to be cracked again using hydrogen in order to increase the kerosene yield. In order to meet the requirements for aviation fuel, the kerosene fraction is refined with various additives. |
Fischer-Tropsch process steps by Anne Rödl (CC BY), adopted by Jana Schultz
Alcohol-to-jet
In order to produce aviation fuel from alcohol, ethanol or butanol must first be produced from sugar. This is done by means of fermentation (bioethanol production), as explained in detail in chapter 2.1 of the HOOU platform's Future Fuels learning offer.
The actual steps of the alcohol-to-jet process are briefly explained in the following table.
Process step | Procedure |
1 | The dehydration process converts alcohol into alkenes by splitting off water. The process is carried out with the addition of sulphuric acid or phosphoric acid and metal oxide catalysts at 170-200°C. |
2 | During the subsequent oligomerization, the alkenes (ethene or butene) combine to form longer-chain molecules. Catalysts are also used here. |
3 | The resulting products are separated by distillation and rectification. |
4 | The subsequent hydrogenation saturates open double bonds with hydrogen to form alkanes. Nickel, palladium or platinum are used as catalysts. The products are kerosene, gasoline and diesel. |
Synthesized iso-paraffins from hydrogenated fermented sugar (SIP)
The production process is based on the metabolization of sugars to long-chain hydrocarbons by genetically modified yeasts. The C-15 alkenes produced are called farnesenes. Various enzymes and fungi are required for this. Basically, this is also a fermentation process that takes place under aerobic conditions, i.e. under the influence of oxygen. The long-chain farnesenes are separated from the fermenter broth and converted into farnesanes via hydrogenation. Sugar-based synthesized iso-paraffins are currently only produced in small quantities, as the process is still in the demonstration phase. It is questionable whether this type of kerosene will actually be used in large quantities.
It is interesting to note that the anti-malarial agent artemisinin, which occurs naturally in annual mugwort, can be biosynthesized as a by-product of the process. The only manufacturer of SIP at present is therefore concentrating more on bio-based chemical products than on kerosene.
Further information on artemisinin and other active plant substances can be found in the book Pflanzliche Arzneimittel.
9.3 From research
- Project report on the use of renewable fuel at Leipzig/Halle Airport
- The use of SAF is being investigated: https://alight-aviation.eu/
- A consortium funded by the EU is currently planning the first alcohol-to-jet production plant.