8. Biogas production
Website: | Hamburg Open Online University |
Kurs: | Process engineering for the bioeconomy |
Buch: | 8. Biogas production |
Gedruckt von: | Gast |
Datum: | Sonntag, 7. September 2025, 07:04 |
Beschreibung
Learn about the biogas production process in this book.
Biogas is seen as an alternative to fossil natural gas. How and from what materials is biogas actually produced? How does the process work and what potential is there?
What you should know
- Which substrates are suitable and what should they be like?
- Which processes take place?
- What equipment is required?
- How can smooth operation be guaranteed?
- Where and how are biogas plants used?
8.1 Substrates
Many organic materials can be used as substrates for biogas production. The decisive factor for the gas yield, i.e. the biogas or methane yield of a substrate, is the content of water, proteins, fats and carbohydrates as well as their digestibility for microorganisms.
Around 47% of the total substrate mass used today are plants such as maize, grass or grain. Animal excrement makes up around 48% of the substrate mass. Waste (3 %) and residual materials (2 %) are also used to a lesser extent. Cattle manure is particularly suitable for starting the fermentation process because it contains a high level of methane bacteria. Chicken manure produces high gas yields, but its high lime and sand content can lead to deposits in the fermenter, which is why it must be pre-treated.
A total area of 1.57 million hectares was required for the cultivation of the plants used in 2021 (FNR 2022). The figure below shows the share of the various crops in the total area under cultivation.
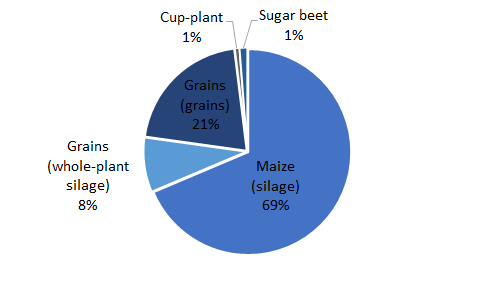
Characterization of substrates
Pararmeter
Important parameters for determining substrate suitability and the required system design are briefly explained below:
Dry matter (DM or Total solids -TS):
Dry matter = total mass minus the water contained
Dry matter content varies greatly with the substrate
Dry matter content between 25 and 35 % ideal
Organic dry matter (oDM or Volatil solids -VS):
only organic substances can be processed by the microorganisms inorganic substances (e.g. minerals) do not contribute to the methane yield, but can still have a negative impact on the decomposition process due to a lack or excess of them
pH value:
The substrate must be neither too acidic nor too alkaline, as otherwise the composition and interaction of the microorganisms will change pH values of 6 to 8 are ideal, because acid is initially produced during methane formation, but the substrate must not become over-acidic
Biochemical oxygen demand (BOD):
Indicator for the content of organic material available for microorganisms, provides an indication of whether aeration is necessary
Chemical oxygen demand (COD):
represents the organic carbon content, an indicator of the theoretical maximum amount of methane that can be produced from a substrate
Total nitrogen content:
Sum of organic nitrogen and ammonium in the sample
measured using the Kjeldahl method (analysis method named after a Danish chemist)
The correct ratio of carbon (C) and nitrogen (N) is very important (C:N ratio). If there is too much carbon in relation to nitrogen, the carbon cannot be fully converted and the methane yield falls short of the maximum possible yield. Too much nitrogen can in turn lead to the formation of ammonia, which has a toxic effect on some microorganisms and can also cause corrosive damage to the system. A ratio of 30:1 to 10:1 of carbon to nitrogen is considered optimal. High protein or nitrogen concentrations can lead to increased formation of ammonia and hydrogen sulphide, which can cause corrosive damage to the system.
A comprehensive list of the properties of various biogas substrates can be found here.
If you want to find out more about the methods for assessing the suitability of substrates, you can read a guide published by the German Biomass Research Center.Impurities
There are a number of other substances that can inhibit the development of microorganisms. These include disinfectants, antibiotics, zinc, copper and surfactants.
8.2 Processes in biogas production
The basic principle of biogas production is simple: substrates that can be degraded by methane-producing microorganisms (methanogenic archaea) are fed into a fermenter and heated. As the methanogens cannot tolerate oxygen, the fermenter must be airtight. The biological decomposition processes produce methane, which is purified and can be burned in gas turbines to generate electricity or heat.
The production of methane (methane fermentation) is mainly carried out by bacteria that live without oxygen. It is an anaerobic decomposition process that also takes place in bogs, for example. The gas produced consists mainly of methane (CH4) and carbon dioxide (CO₂). Not just one type of bacteria is involved in the process. The different strains are dependent on each other and each carry out sub-steps of the degradation process. The initial substrate determines the composition of the bacterial community, with the bacteria with the lowest growth rates limiting the speed of degradation and thus methane formation.
The methane formation process
In general, a distinction is made between four sub-processes, which do not take place separately, but in parallel in terms of space and time.
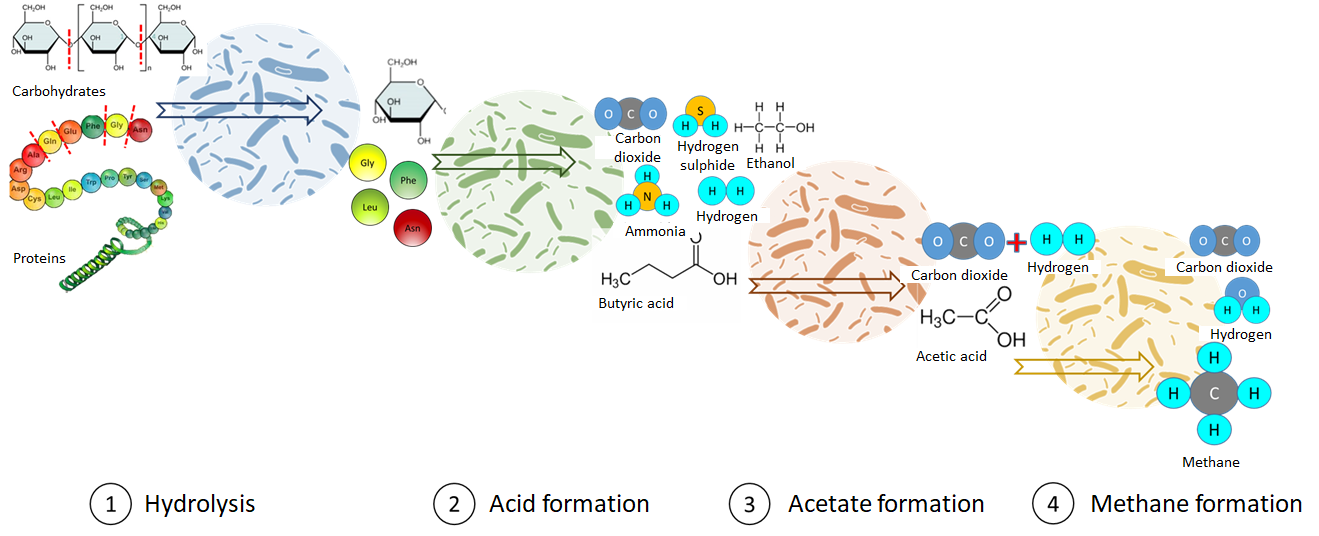
1st step = hydrolysis:
Breakdown of polymeric organic components (proteins, fats, carbohydrates) into small water-soluble monomers (amino acids, fatty acids, mono- and disaccharides). The degradation rate of the components usually also determines the speed of the overall process. Cellulose, for example, is more difficult for microorganisms to break down.
2nd step = acidification:
Acid-forming, facultatively anaerobic bacteria metabolize monomers into short-chain carboxylic acids (butyric or propionic acid), alcohols (ethanol) and gases (CO₂, H2, hydrogen sulphide and ammonia)
3rd step = acetate formation:
Acetogenic, heat-loving bacteria convert the carboxylic acids into acetic acid, hydrogen and carbon dioxide
4th step = methane formation:
Methane bacteria (archeobacteria) break down acetic acid in an anaerobic environment or reduce carbon dioxide using hydrogen. Methane is formed 70% from acetic acid and 30% from the reaction of carbon dioxide and hydrogen.
Conditions in the fermenter
A constant temperature should prevail in the fermenter. Rapid temperature changes disrupt the development of the microorganisms and destabilize the process. The ideal temperature for the development of microorganisms is 36-38 °C. The highest gas yields and stable operation are achieved in this mesophilic range. However, there are also fermenters that operate at ambient temperature (<25 °C) or in the thermophilic range of 50° to 60 °C.
Although the methane-forming microorganisms are sensitive to oxygen, contact with oxygen can never be completely prevented in practice. However, since oxygen-consuming bacteria also live in the fermenter, the oxygen is used by them before it can damage the archaea. However, too much oxygen must not be allowed to enter the fermenter.
The pH value should also be set correctly. A pH value of 7 is ideal. Acid inhibits the development of methane-producing bacteria and pH values that are too high (> 8) have a toxic effect. The pH values are mainly determined by the substrate. If the fermenter is overfilled due to an incorrect ratio of substrate supply, temperature and microbial activity, acidification can occur.
Helpful information for planning a biogas plant can be found here.
Residence times
- depending on the substrate
- for short periods of time, only easily degradable substances are methanized
- with longer periods, medium to poorly degradable substances are also methanized
- longer residence time means higher gas yield per kg of biomass
- the residence time also depends on the reactor volume
- however, complete degradation would take a very long time and require large plant volumes
- an optimum degradation performance should therefore be found
- Important key figure for the dimensioning of the plant: OLR organic loading rate (in kg oTS/m3 x d) - possible supply of organic dry matter (oTS) per time unit and reactor volume
- the higher the room loads and lower the substrate concentration, the lower the retention time in the reactor
- highest gas production rate at the operating point of the smallest practically possible residence time that can be operated stably
8.3 Biogas plant technology
Basically, biogas plants can be divided into 2 superordinate groups (wet fermentation and dry fermentation); there are no sharp boundaries between the processes and there are a variety of design options within both superordinate groups.
In any case, the basis for successful anaerobic fermentation is the conditioning of the biomass to be fermented (substrate). This can vary depending on the fermentation technology used. Common conditioning steps are:
- raw material cleaning, in which impurities (e.g. sand, stones, tool parts) are separated,
- raw material shredding to make the nutrients more easily accessible for the microorganisms and, if necessary
- raw material storage, which is also carried out in the absence of oxygen (anaerobic) with a view to subsequent anaerobic fermentation in order to prevent aerobic decomposition processes.
In addition, care must be taken to ensure that the substrate does not contain any substances that could inhibit bacterial growth (such as disinfectants from the animal product processing industry).
Wet fermentation refers to fermentation processes in which the dry content of the substrate in the reactor is a maximum of 15 to 20 % in relation to the fresh mass. The diagram of a wet fermentation plant in stirred tank reactor design is shown in the following figure.
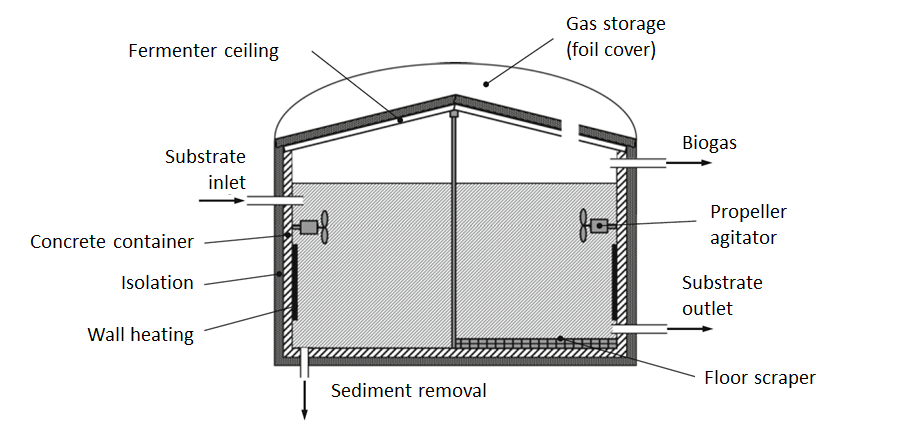
In terms of system technology, a continuous solution is preferable for the substrate feed. This is realized for pumpable substrates via electric pumps and for stackable substrates via, for example, screw conveyors, push floors or even flushing. When feeding, care must be taken to ensure that the temperature difference between the reactor contents and the substrate is not too great so as not to disrupt anaerobic degradation.
To maintain the mass balance in the reactor, the same amount of fermentation residue and biogas must be discharged from the reactor as is fed into it as substrate. Care must be taken to ensure that the residence time of the substrate in the reactor is at least as long as the doubling rate of the microorganisms, as otherwise their concentration in the reactor would continuously decrease.
Furthermore, it must be prevented that the added substrate is directly discharged again. In the reactor shown in the figure (diagram of a wet fermenter), this is achieved by spatially separating the substrate feed and discharge. However, it is not possible to completely prevent direct discharge due to micro-currents in the reactor; in most cases, however, the quantities of substrate immediately discharged again are negligible.
In order to provide the microorganisms with degradable biomass at all times and to ensure a uniform temperature distribution, mixing systems are installed in the reactors. In the figure (diagram of a wet fermenter) this is realized by propeller agitators. Other options for mixing include substrate pumps, gas mixing or large-wing agitators.
The biogas is collected in the head area of the reactor and can be extracted from there. The reactors are often equipped with an integrated biogas storage tank to enable variable biogas extraction.
Another type of fermentation technology is dry fermentation, also known as solids fermentation. In contrast to wet fermentation, only stackable biomass with a dry content greater than 15-20% is fermented. Feeding can be discontinuous or continuous. Both variants are shown schematically in the following illustration.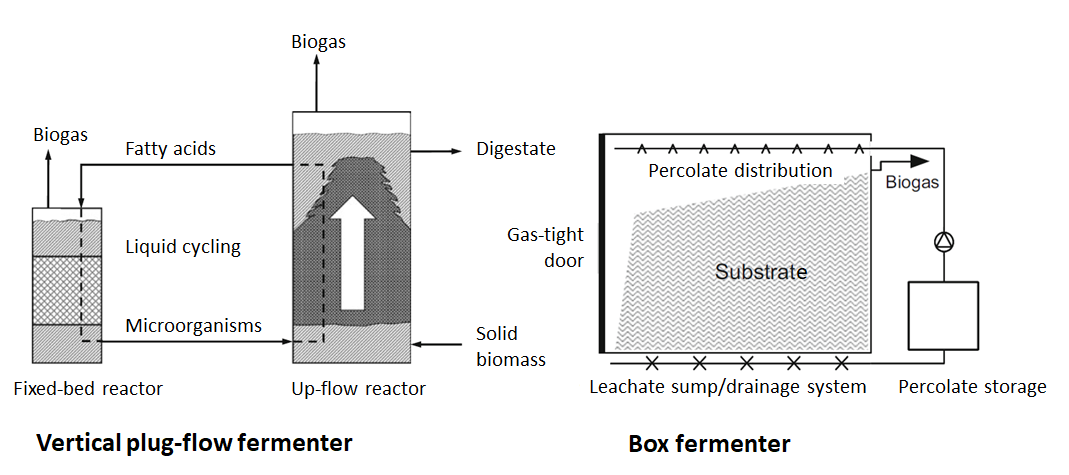
In discontinuous fermentation, the biomass is fed into the box or garage fermenter (figure (diagram of dry fermentation), right) using a front loader, for example, and the fermenter is then sealed gas-tight.
Anaerobic fermentation is supported by the recirculation of the leachate. The leachate, which contains microorganisms and organic substances, is first stored in a tank - the substrate is then irrigated with this leachate. The leachate is also referred to as percolate (by definition, this is a liquid that flows through a solid). Irrigation with percolate results in the mixing of microorganisms and fresh substrate. No further mechanical mixing of the substrate takes place.
8.4 Possible applications of biogas
There are two possible uses for biogas:
1. direct energy use
The biogas is burned directly in a combined heat and power plant (CHP) without pre-cleaning. In a CHP unit, the resulting energy is first converted into mechanical energy using the principle of a combustion engine and then into electrical energy in a generator. In addition, the resulting heat can be used to provide space heating, for example.
2. use in the form of biomethane
Biogas can be converted into biomethane (preferably pure methane gas) using purification processes. When converting biogas into biomethane, various impurities must be separated. The sequence of the individual purification steps is shown schematically in the following diagram.
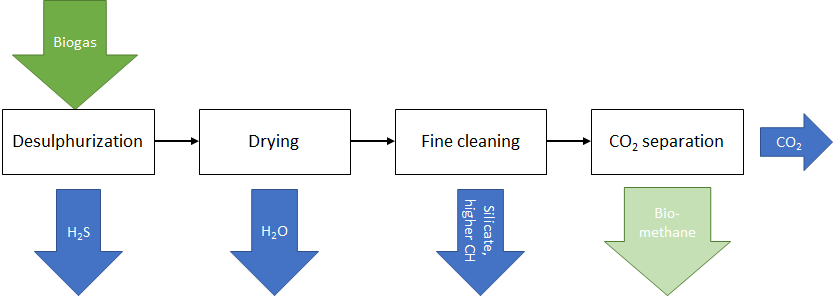
1st step = hydrolysis:
The sequence of these conversion steps is not fixed and can vary depending on the process used.
During desulphurization, the hydrogen sulphides are first separated from the gas flow. These can be removed biologically via aerobic sulphur bacteria or chemically via a chemical reaction with the addition of sulphur-binding substances or by chemical binding to the surfaces of surface-active solids (so-called adsorption).
The biogas can be dried, for example, by refrigeration drying (also known as condensation drying), whereby the water precipitated by the cooling of the gas flow is removed.
The separation of higher hydrocarbons, as well as dust and silicates, is referred to as fine purification. This separation can be achieved by using activated carbon in a fixed bed reactor.
In the final step, CO2 is separated from the biogas stream. Usually, the CO2 was then emitted into the atmosphere. However, the demand for green CO2 has been growing in recent years for a variety of applications, such as applications in greenhouses, in the beverage industry and in the chemical sector. It can therefore be assumed that CO2 will continue to be utilized in the future.
There is also the possibility of converting CO2 into methane using chemical or biological processes in order to increase the biomethane yield.
The gas stream remaining after CO2 capture then consists of almost pure methane, which can be used for material or energy purposes.