8. Biogas production
8.3 Biogas plant technology
Basically, biogas plants can be divided into 2 superordinate groups (wet fermentation and dry fermentation); there are no sharp boundaries between the processes and there are a variety of design options within both superordinate groups.
In any case, the basis for successful anaerobic fermentation is the conditioning of the biomass to be fermented (substrate). This can vary depending on the fermentation technology used. Common conditioning steps are:
- raw material cleaning, in which impurities (e.g. sand, stones, tool parts) are separated,
- raw material shredding to make the nutrients more easily accessible for the microorganisms and, if necessary
- raw material storage, which is also carried out in the absence of oxygen (anaerobic) with a view to subsequent anaerobic fermentation in order to prevent aerobic decomposition processes.
In addition, care must be taken to ensure that the substrate does not contain any substances that could inhibit bacterial growth (such as disinfectants from the animal product processing industry).
Wet fermentation refers to fermentation processes in which the dry content of the substrate in the reactor is a maximum of 15 to 20 % in relation to the fresh mass. The diagram of a wet fermentation plant in stirred tank reactor design is shown in the following figure.
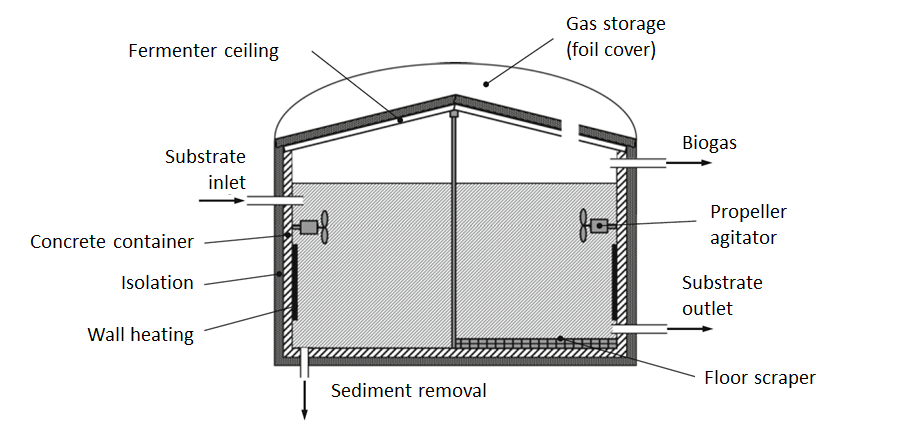
In terms of system technology, a continuous solution is preferable for the substrate feed. This is realized for pumpable substrates via electric pumps and for stackable substrates via, for example, screw conveyors, push floors or even flushing. When feeding, care must be taken to ensure that the temperature difference between the reactor contents and the substrate is not too great so as not to disrupt anaerobic degradation.
To maintain the mass balance in the reactor, the same amount of fermentation residue and biogas must be discharged from the reactor as is fed into it as substrate. Care must be taken to ensure that the residence time of the substrate in the reactor is at least as long as the doubling rate of the microorganisms, as otherwise their concentration in the reactor would continuously decrease.
Furthermore, it must be prevented that the added substrate is directly discharged again. In the reactor shown in the figure (diagram of a wet fermenter), this is achieved by spatially separating the substrate feed and discharge. However, it is not possible to completely prevent direct discharge due to micro-currents in the reactor; in most cases, however, the quantities of substrate immediately discharged again are negligible.
In order to provide the microorganisms with degradable biomass at all times and to ensure a uniform temperature distribution, mixing systems are installed in the reactors. In the figure (diagram of a wet fermenter) this is realized by propeller agitators. Other options for mixing include substrate pumps, gas mixing or large-wing agitators.
The biogas is collected in the head area of the reactor and can be extracted from there. The reactors are often equipped with an integrated biogas storage tank to enable variable biogas extraction.
Another type of fermentation technology is dry fermentation, also known as solids fermentation. In contrast to wet fermentation, only stackable biomass with a dry content greater than 15-20% is fermented. Feeding can be discontinuous or continuous. Both variants are shown schematically in the following illustration.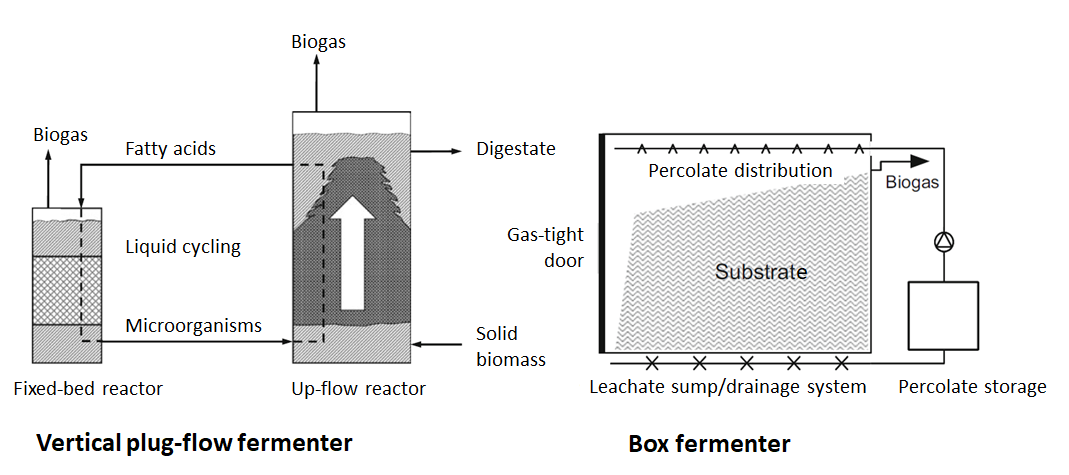
In discontinuous fermentation, the biomass is fed into the box or garage fermenter (figure (diagram of dry fermentation), right) using a front loader, for example, and the fermenter is then sealed gas-tight.
Anaerobic fermentation is supported by the recirculation of the leachate. The leachate, which contains microorganisms and organic substances, is first stored in a tank - the substrate is then irrigated with this leachate. The leachate is also referred to as percolate (by definition, this is a liquid that flows through a solid). Irrigation with percolate results in the mixing of microorganisms and fresh substrate. No further mechanical mixing of the substrate takes place.