Global Supply Chain and Logistics
4. Design of the supply chain
On this page, you will learn, how to design a supply chain and what different aspects need to be considered in this complex process.
Consumers drive the whole system of goods movement as concerns the demand side.
We are (partly) responsible for the use of exhaustible resources and the impact on the environment.
But we cannot do without consumption either: we need something to eat and drink, some clothes to keep warm and some kind of housing.
Supply chains are needed to meet the demand for these goods and commodities. In these supply chains many different stakeholders with different expectations are involved. To realize the flow of goods from the point of origin to the point of destination, supply chains need transport vehicles as well as facilities for storage and handling.
- Typical vehicles for long distance transport are airplanes and seagoing vessels, for regional transport inland waterway vessels, trains and trucks.
- For the last mile delivery vans are common.
- The transshipment between the transport vessels takes place in logistic nodes, as ports, airports or other freight terminals.
How do logistics strategies influence the freight transport system?
The following figure "Competitive strategy of a company" shows, how the supply chain strategies, the steering schemes and the supply chain structure influence the competitive strategy of a company. All influencing parts are described in detail below. “The goal is to structure the drivers to achieve the desired level of responsiveness at the lowest possible cost, thus improving the supply chain surplus and the firm’s financial performance." (Chopra & Meindl, 2016, p. 56)
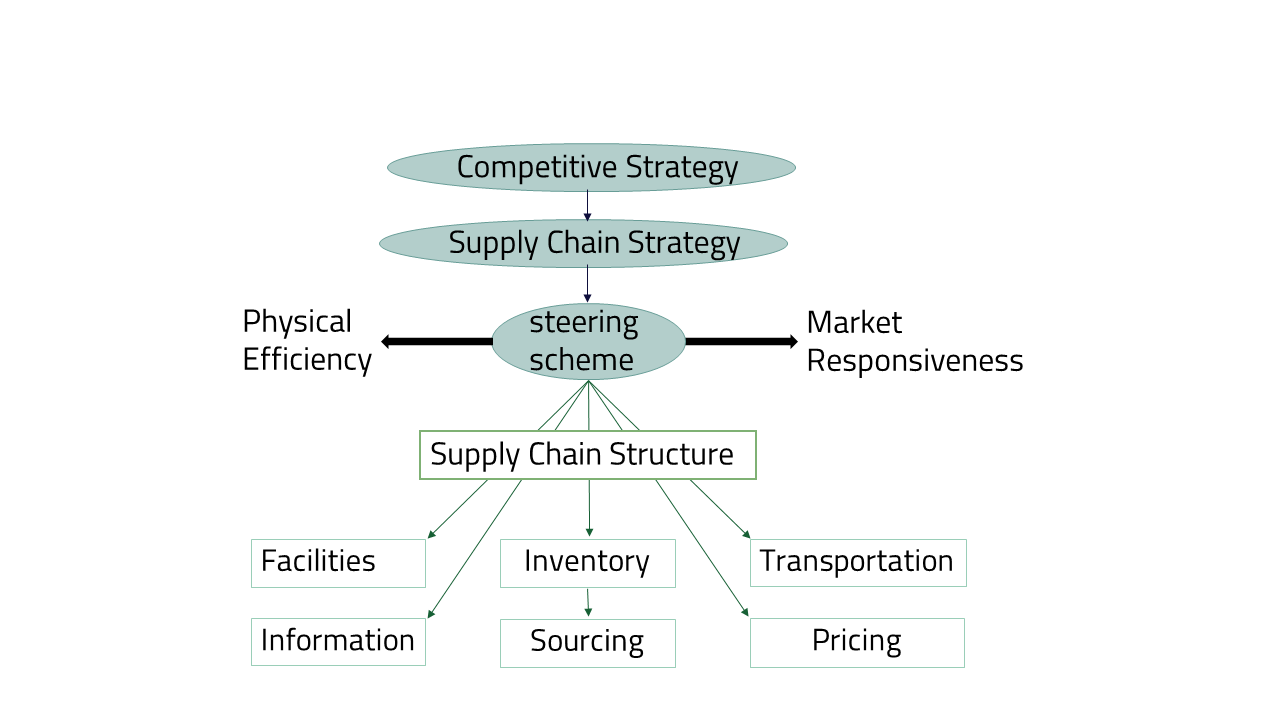
Supply chain strategies
The supply chain strategies of the companies are focussing on the balance between responsiveness and efficiency that results in strategic fit with the competitive strategy that matches the needs of the customer best (Chopra & Meindl 2016, p. 46, 56).
The combined impact of the drivers “facilities, inventory, transportation, information, sourcing and pricing” determine the grade of market responsiveness.
The supply chain structure is directly connected to a steering scheme: This means mainly: Is the company able to meet the market requirements in terms of quality and quantity, at the right time and the right place?
At the same time it is necessary to realise the highest physical efficiency of the (entire) supply chain to minimize their total cost.
Steering schemes
Regarding supply chain strategies, there are generally two targets for using the new steering principles of logistics and supply chain management (Chopra & Meindl, 2016, p. 56):
- the reduction of stocks throughout the supply chain and thereby, the reduction of the so-called "Bullwhip-Effect" (physical efficiency)
- avoiding out-of-stock-situations and associated opportunity costs (market responsiveness).
These targets can be achieved by generating minimal costs, considering storage costs, capital commitment costs and mobilizing economies of scale (Bowersox 2007, pp.12).
The central idea behind steering concepts is to reduce or even eliminate the total stock of product units within the supply chain at a certain time and to produce customer-oriented goods.
The process of steering is determined by two basic principles:
- the temporal adjustment of the value adding processes (time based) via flow-oriented or resource-based (functional) approaches;
- the nature of the order, further distinguished by push and pull steering modes.
Both two steering approaches tend to influence
- the magnitude of freight flows,
- its temporary urgency and
- patterns of spatial distribution of those activities required to cope with the demand.
Resource or flow oriented
The figure "Ressource and flow oriented steering approach" shows the differences between the two approaches.
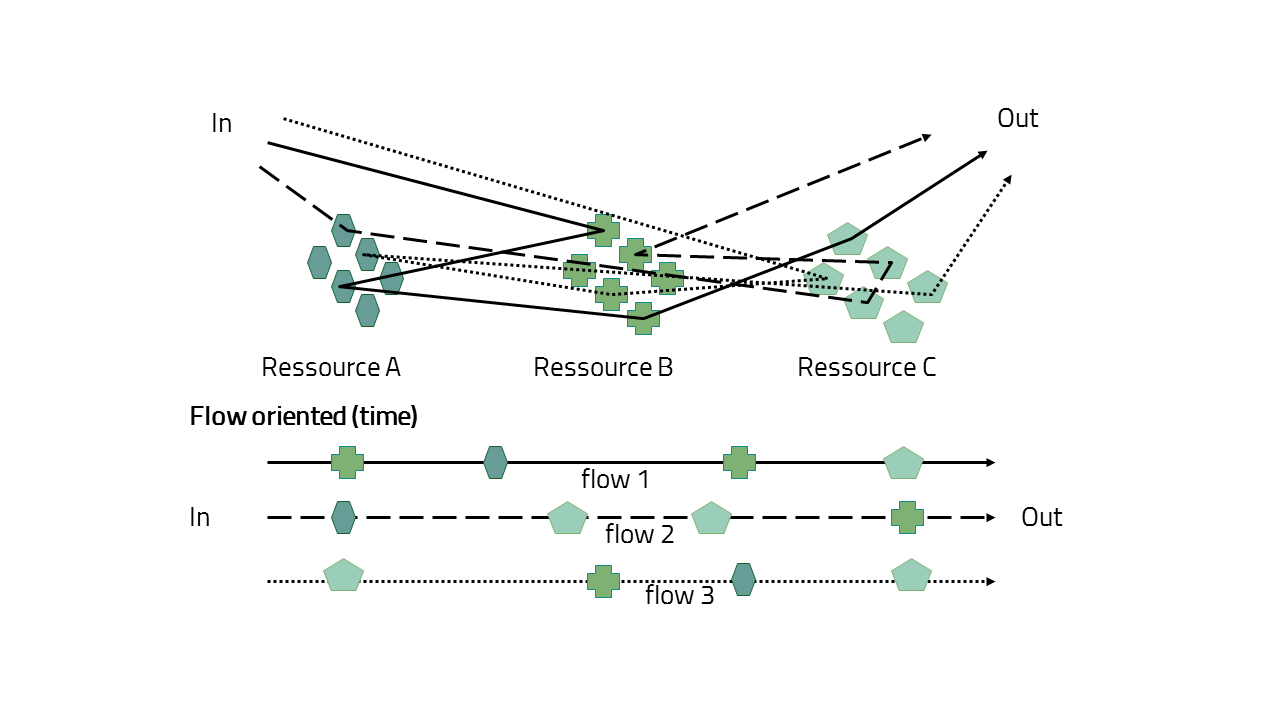
- In the flow-oriented approach, steering is organized via the time that is required for certain tasks to be done. The central steering parameter is the lead time which has to be kept at a minimum.
- In the resource-oriented approach, steering is organized via the available capacities of resources and the time that is required for getting certain tasks done; these capacities can comprise e.g., machinery or staff capacity.
- In logistic transport systems, this approach is of importance for large logistics nodes, such as harbours, freight transport centers, goods distribution centers with major warehouses and consolidation outlets. They tend to be crucial for the functionality of these nodes. However, some specialized interfaces may only be suitable for meeting very specific demands.
- A standardized production system, which is found in the case of hubs of courier, express and postal (CEP) service providers, is adjusted to a consistent use of capacity with standardized shipment (dimensions, weight) and covers only forwarding (no storage or commissioning) and the function of consolidating transport.
Push- or pull-oriented
The figure "Push- and pull-principle" shows the two different steering approaches. Steering the supply chain by means of the type of order is closely connected to the point of time of the individual customer’s order, the so-called "Order Penetration Point" (Sharman 1984, p. 73).
At this point, the final product is individualized and in most cases its destination is known.
At this point, the final product is individualized and in most cases its destination is known.
In the case of mass products, the order penetration point is not used for steering purposes. Regarding customer-independent production, goods are being delivered out of the warehouse. The production follows the push-principle: it is forecast-based and will be steered by a plan outside the production system (Hopp & Spearman, 2001, p. 340).
In the case of customer specific products, i.e. in the ship building-industry, the customer is supplied directly, avoiding storage (contract manufacturing). In such pull-systems, the steering occurs via the status of the system itself (Hopp & Spearman, 2001, p. 340).
After deciding on the steering scheme, the company needs to decide, which kind of supply chain structure is the most useful in supporting your steering scheme.
Supply chain structure
Regarding goods flow systems, there are generally two groups: direct and indirect systems, which are shown in the figure "Supply chain structure".
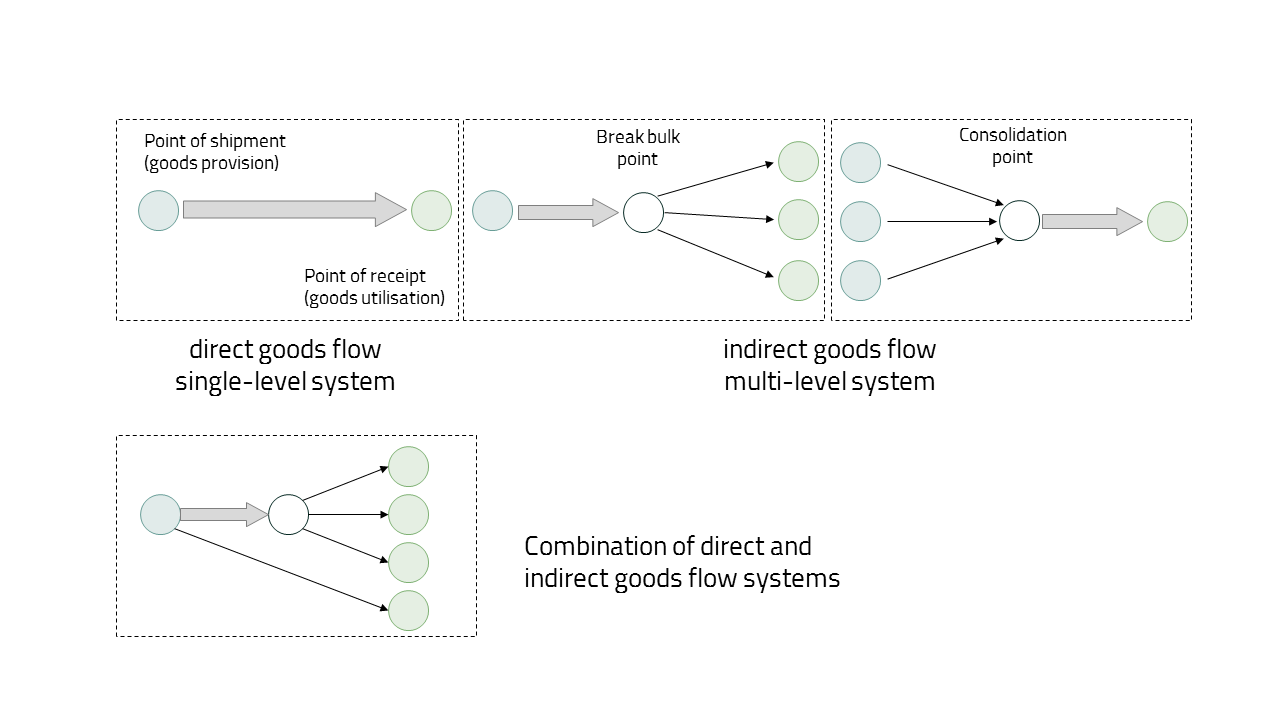
Direct flow systems are characterized by two existing interfaces: one at the origin and one at the destination of a transport chain. Goods are transported directly from the sender to the recipient. There is no interruption within the supply chain.
In indirect flow systems the goods flow is interrupted by various trade levels, changing loading units or transport mediums in order to bundle shipments (consolidation) and thereby, increasing the efficiency of the system. Thus vehicles can be used to their full capacity. Additionally, more efficient means of transportation can be used. Concerning transport management, transport is either realized through direct transport or through grid patterns or so-called "Hub-and-Spoke" (HuB)-Systems. In grid patterns, handling points are exclusively connected by direct transport. In the case of general cargo, cooperation’s are often organized this way.
In indirect flow systems the goods flow is interrupted by various trade levels, changing loading units or transport mediums in order to bundle shipments (consolidation) and thereby, increasing the efficiency of the system. Thus vehicles can be used to their full capacity. Additionally, more efficient means of transportation can be used. Concerning transport management, transport is either realized through direct transport or through grid patterns or so-called "Hub-and-Spoke" (HuB)-Systems. In grid patterns, handling points are exclusively connected by direct transport. In the case of general cargo, cooperation’s are often organized this way.
The consolidated main transport flow between two hubs is indicated by the bold arrow in the figure on the right, while the small arrows symbolize consolidating or distributing transport on the so-called first and last mile.
Now you know how to design a supply chain.
Literature
- Bowersox, D.J.; Closs D. J.; Cooper M. B.; Bowerbox, J. C. (2007): Supply Chain Logistics Management. 2nd Edition. McGraw-Hill/Irwin, NY.
- Chopra, S.; Meindl, P. (2016): Supply chain management (3. ed., Pearson internat. ed.). Upper Saddle River, NJ: Pearson Prentice Hall.
- Hopp, J. W.; Spearman, M. L. (2001): Factory Physics: Foundations of Manufacturing Management. 2nd Edition. McGraw-Hill/Irwin, NY
- Löwa, S.; Flämig, H. (2011): Integration of Logistics Strategies in Urban Transport Models In: Conference Proceedings of 4th METRANS „National Urban Freight Conference“, Long Beach, CA (USA)
- Pfohl, H.-C.(2004): Logistiksysteme - Betriebswirtschaftliche Grundlagen, Berlin, Heidelberg, New York, Springer-Verlag, 7. Auflage.
- Sharman, G. (1984): The rediscovery of logistics. Harvard Business Review 62(5)