4.3 Applications in the Industry Sector
Steel Making
The most important raw material for steel production is naturally occurring iron ore. Iron ores used for steel production today are mostly iron oxides - in other words, chemical compounds of iron with oxygen (e.g. iron(III) oxide, Fe2O3). In order to to produce steel, the iron must be separated from the oxygen. In the classic blast furnace process, the oxygen is separated with the help of coke, a fuel made from coal. The following reaction equation is a simplified representation of the chemical process taking place:
Fe2O3 + 3 CO --> 2 Fe + 3 CO2
The carbon contained in the coke acts as a so-called reducing agent and reacts with the oxygen from the iron oxide at first to form carbon monoxide and later carbon dioxide. In addition, the coke provides the energy needed to reach the temperatures of up to 1600 °C in the blast furnace required to reduce the iron ore. So-called pig iron is produced in the blast furnace. This pig iron contains many by-products such as sulfur, phosphorus and carbon and generally cannot be used directly. The pig iron is processed into crude steel in the oxygen converter, where the undesirable by-products are removed with the help of oxygen.
Steel production using the blast furnace route is a very CO2-intensive process. Steel production alone, currently, accounts for approximately 6 % of Germany's total greenhouse gas emissions.
Steel production using the blast furnace route is a very CO2-intensive process. Steel production alone, currently, accounts for approximately 6 % of Germany's total greenhouse gas emissions.
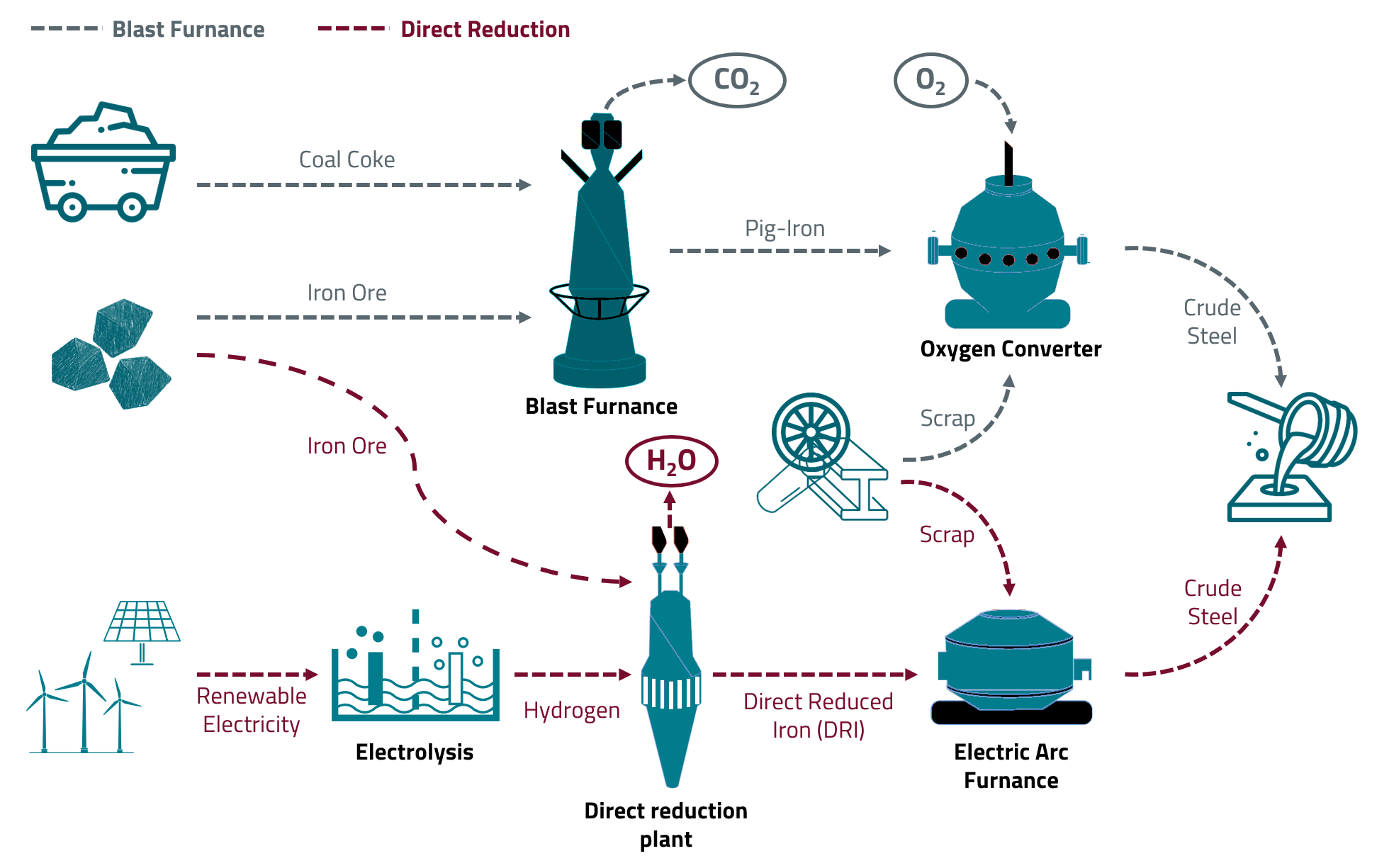
Fe2O3 + 3 H2 --> 2 Fe + 3 H2O
The product of the direct reduction process is a material called sponge iron. Similar to the pig iron from the blast furnace the sponge iron usually contains various impurities such as sulfur or phosphorus. The separation of impurities and further processing into crude steel is carried out in electric arc furnances. In this process, the sponge iron is heated to up to 3000 °C using electrical energy. Electric arc furnaces are already used on an industrial scale today and are mainly applied for the processing of steel scrap and the production of quality and stainless steels. The direct reduction of iron ore with the help of hydrogen, though, has not yet been realised on an industrial scale. Various steel manufacturers have announced pilot projects and expect to be able to produce climate-neutral steel using hydrogen by 2030 at the latest.
The combination of hydrogen-based direct reduction and electric arc furnance makes it possible to produce steel exclusively on the basis of renewable energies. However, the electricity demand of this production route (for the production of the green hydrogen and the operation of the electric arc furnace) is enormously high. If Germany's entire steel production (approx. 40 million t/a) were to be converted to the hydrogen route, around 190 TWh of electrical energy would be required annually. This corresponds to more than one third of Germany's total current electricity consumption.